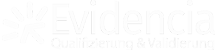
Do you have any questions on machine validation?
Do you need a quotation?
Do you have any other requests or suggestions?
If so, simply complete the enquiry form and click on “Send”.
We will get in touch with you immediately.
The term qualification refers to an individually adaptable and structuring method for testing equipment during a new acquisition or modification.
Qualification aims to provide evidence that the equipment is suitable for its intended purposes and meets the specified requirements. This is to ensure the safety and efficacy of manufactured products. Qualification is carried out using standardized and predefined procedures, and the results are documented to ensure traceability and accountability.
This is a step-by-step process:
> DESIGN QUALIFICATION
> INSTALLATION QUALIFICATION
> OPERATION QUALIFICATION
> PERFORMANCE QUALIFICATION
Qualification is conducted in phases, as described in the diagram below. The User Requirement Specification (URS) defines the requirements for the planned or to-be-acquired equipment. The Design Qualification (DQ) ensures that the device is designed and constructed according to the requirements. The Installation Qualification (IQ) verifies that the device has been correctly installed and connected. The Operational Qualification (OQ) tests whether the device functions as intended, and the Performance Qualification (PQ) ensures that the device delivers the desired performance.
Qualified equipment and validated processes form the basis for flawless functionality and high productivity in practice. We are happy to support you in implementing this in your company.
We not only offer the suitable measurement equipment for conducting your qualification but also specialized technical know-how and detailed knowledge of standards, directives and guidelines.
We advise you on the acquisition of new equipment and accompany you from the beginning to the start of operation with competence and many years of experience. Our team of highly trained technicians and qualification engineers efficiently and reliably carry out the qualification of your equipment. We create GLP and GMP compliant documentation for equipment qualification and process validation, requalification, heat distribution reports, process evaluations, and provide advice in these areas.
We look forward to being your competent partner throughout the entire qualification process with our expertise!
———————————————————————————————————————————————————————————————————-
Contents of the tests:
In this phase, the user defines the requirements for the planned equipment. In addition to process requirements, laws, standards, and guidelines to be considered as well as internal company specifications should be taken into account.
The URS is the basis for qualification. The requirements defined here are to be tested in the coming phases.
———————————————————————————————————————————————————————————————————-
Based on the requirements defined in the URS, a comparison is made with the manufacturer’s specifications to ensure that the requirements placed on the euqipment are met and that the characteristics of the planned equipment correspond to the predefined requirements.
The aim is documented verification that the equipment is designed as ordered.
———————————————————————————————————————————————————————————————————-
During IQ, it is verified that the equipment has been correctly assembled and installed. In addition, the physical characteristics of the delivered equipment are verified. This includes the completeness of the delivery, the clear identifiability of the equipment and its parts, and the equipment configuration according to specification.
The aim is to provide documented evidence that a system/equipment has been delivered and installed in accordance with the specifications.
———————————————————————————————————————————————————————————————————-
During OQ, documented proof is provided that the device complies with the requirements and specifications for functionality. For this purpose, both triggering conditions for safety features and machine states that can lead to program aborts and error messages are simulated. The equipment is run empty in this phase.
The aim is to provide documented proof that a system functions according to specifications without any product being introduced.
———————————————————————————————————————————————————————————————————-
In this phase, the performance of the equipment is verified according to the specifications. The objective is to provide documented evidence that the specified process requirements are adequately met under actual conditions. The unit is performed here as it is performed in day-to-day business.
The aim is to provide documented proof that the unit operates according to the specifications with the product introduced.